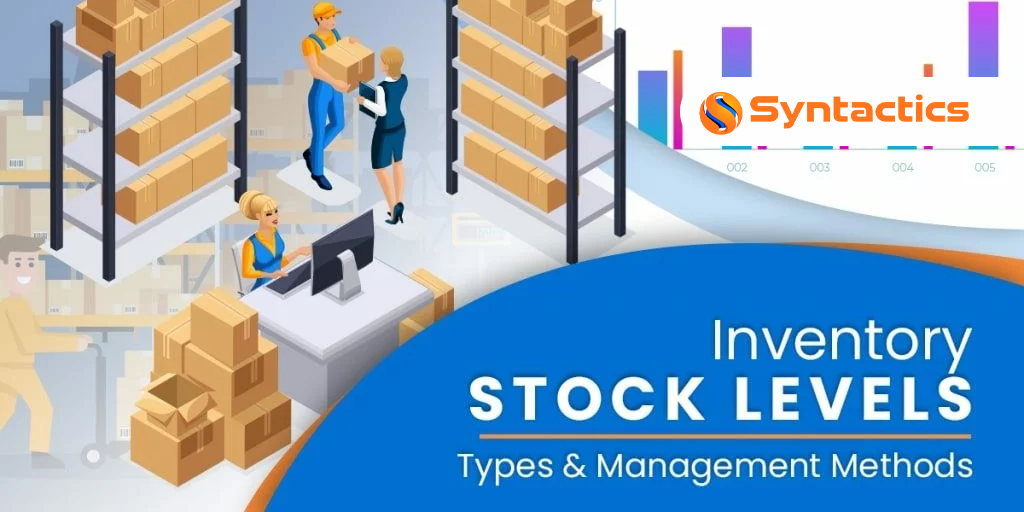
Inventory Stock Levels: Different Types and Effective Management Methods
The products you have stocked in your inventory are crucial to your business. Leaving them unattended or unaccounted for will result in losses in the long run. Moreover, this could cause issues with your Inventory Stock Levels.
Though we continue to innovate many devices we use daily, most of their previous counterparts have become obsolete. Stocks left in your inventory for far too long may also experience the same fate. Thus, it’s necessary to be able to sell them off in the most efficient way possible.
However, “43% of small businesses” don’t habitually track their inventory. But before learning how to manage your stock levels, you must first know its four types.
Inventory Stock Levels
Inventory Stock Levels refer to the quantity of products or materials a business has in its inventory at a given point. As a result, they’re crucial for businesses. There are four primary stock levels that businesses need to manage:
- Minimum;
- Maximum;
- Danger and
- Average.
Effective stock management means meeting customer demand while minimizing carrying costs. It involves the following aspects:
- Continuous monitoring of stock levels;
- Making adjustments as needed and
- Balancing between the various levels.
The Four Types Of Inventory Stock Levels
The first two types are the minimum and maximum stock levels. True to their name, they provide a definite range on the number of products you should have. Failing to stay within that range could leave you in one of two scenarios. Neither of them is good for your company.
Minimum Stock Levels
To ensure uninterrupted workflows, your business must maintain minimum inventory levels. Failing to meet your minimum stock level could easily result in a shortage of supplies.
Minimum inventory levels may differ from business to business. But, there are a few factors that determine the minimum level:
- The type of material;
- Lead time;
- Rate of consumption and
- Reordering level.
Maximum Stock Levels
On the other hand, exceeding the maximum stock level amount can be a definite identifier that you’re overstocking. Experiencing minimum levels means you may fail to meet your clients’ product demand. However, maximum stock levels mean you have too many products left in stock, which are at risk of becoming obsolete.
Of course, extra inventory leads to high storage costs, discrepancies, and disorganization. Here are some critical considerations when fixing maximum levels:
- Availability of storage space;
- Carrying cost of inventory;
- Risk related to pilferage, obsolescence, and deterioration of raw materials;
- Government restrictions;
- Changes in consumer demand, and more.
Fortunately, the remaining two types can help you further optimize your stock levels.
Average Stock Levels
An average stock level is the amount of stock or raw materials in the company’s warehouse at any time. To ascertain this stock level, it’s essential to set a distinct Reorder Point (ROP) for each product.
Use your ROP to guide you when identifying a definite supply reorder date, whether they’re raw goods or finished items.
Source: G2.
Danger Stock Levels
Finally, there’s the danger level, which warns you it’s time to reorder. It’s usually established as a specific point between your minimum and average levels. However, other companies acknowledge their products have hit the danger level when they reach their minimum stock level.
Businesses should avoid this level at all costs since it indicates a possible stockout. As a result, companies have to expedite more materials, which means you need to spend the following:
- Spending extra fees;
- Transportation charges and
- Overall inventory costs.
Consider various factors, such as your suppliers’ estimated delivery time, before you set your danger stock level.
Now that you’re familiar with the four types, you can begin incorporating them into your inventory management methods.
Inventory Management Methods For Optimizing Your Inventory Stock Levels
Companies often double-check whether the items in their warehouses or stores match inventory records at year-end. This process, commonly known as inventory reconciliation, is critical to your overall inventory management process.
Source: Statista.
Previously, Wasp Barcode surveyed over 1,100 Small and Medium-sized Businesses (SMBs). According to the results, 46% of these SMBs either manually track their inventory items or don’t track them at all. And with the lack of automation, this can easily become one of the company’s most time-consuming processes.
Fortunately, “73% of organizations” planned to equip workers with mobile devices to begin modernization. But to fully optimize your Inventory Stock Levels and minimize the discrepancies in your records, consider the following:
Safety Stock Inventory
Other companies utilize the Safety Stock Inventory technique. Also known as Buffer Stock, these are extra products you keep on hand to mitigate emergencies.
Buffer Stock is handy when your supplier can’t deliver your goods on time. Additionally, it’s helpful when more clients are purchasing your products than expected.
LIFO
The Last In, First Out (LIFO) method requires that companies sell newly acquired goods first. As a result, companies who use it work their way backward. Consequently, a business sells the first batch of goods it acquired after selling all other batches.
It allows companies that sell non-perishable goods to increase their profit. After all, they’ve acquired them at lower prices than their current market value.
FIFO
The First In, First Out (FIFO) method follows the general principle that goods ordered first are sold quickly. Companies often have their own FIFO Inventory System customized to their needs to manage their inventory and sales more efficiently.
Talk to Us About the Ideal Business App for Your Needs Today!
You can also optimize your inventory stock levels by incorporating a few strategies from the previous methods into your system. Its real-time updates on your inventory amounts are essential for demand forecasting.
This is an advantage, considering that not having a helpful management tool is one of business inventory management’s challenges. In turn, you’ll minimize the risks of having a shortage or overstocking your products. As a bonus, FIFO is also authorized by the Generally Accepted Accounting Principles (GAAP) and International Financial Reporting Standards (IFRS).
Batch Tracking
For products manufactured and sold in bulk, companies can perform Batch Tracking. With this method, manufacturers can assign a single expiry date to a group of products made simultaneously. It ultimately results in a more optimized product monitoring system and inventory stock levels for food wholesalers.
How Will You Optimize Your Inventory Stock Levels in 2024?
Ultimately, closely monitoring your Inventory Stock Levels is the most effective way to optimize them. Make it a point to combine the right inventory management software and forecasting techniques. As a result, you accurately forecast the number of goods to order from your supplier.
Additionally, you must compute the average stock levels of your products. It can also serve as one of your bases for demand forecasting during your company’s operations. Learn more about other inventory management and analysis methods, such as the following:
- ABC;
- FSN;
- VED;
- HML and
- SDE.
The ideal Online Inventory Management System can generate reports. But, the data you receive from reports should also be complemented by your intuition.
While your inventory management software can generate reports it’s important to note that the data you receive from reports should also be complemented by your own intuition.
With an informed idea of the actual and estimated demand for your products, you’ll be able to easily identify the appropriate stock levels and inventory management methods to use for your company.
Comment 0